PDC Bit full name is Polycrystalline Diamond Compact Bit,which is one of the most important material advances for oil drilling tools in recent years. Fixed-head bits rotate as one piece and contain no separately moving parts. When fixed-head bits use PDC cutters, they are commonly called PDC bits. Since their first production in 1976, the popularity of bits using PDC cutters has grown steadily, and they are nearly as common as roller-cone bits in many drilling applications.Nowadays, when consider all the drilling depth in all industries ( Oil and Gas, Water well, Geothermal, HDD etc), it takes more than 60%.
PDC bits are designed and manufactured in two structurally dissimilar styles ,Matrix Body Bits & Steel Body Bits. The two provide significantly different capabilities, and, because both types have certain advantages, a choice between them would be decided by the needs of the application.It is now widely known as PDC drill bits are available in both matrix as well as steel bodies. Those who are new to the drilling industry may often get confused when it comes to deciding which one should be used when. Here is some information that might come in handy.
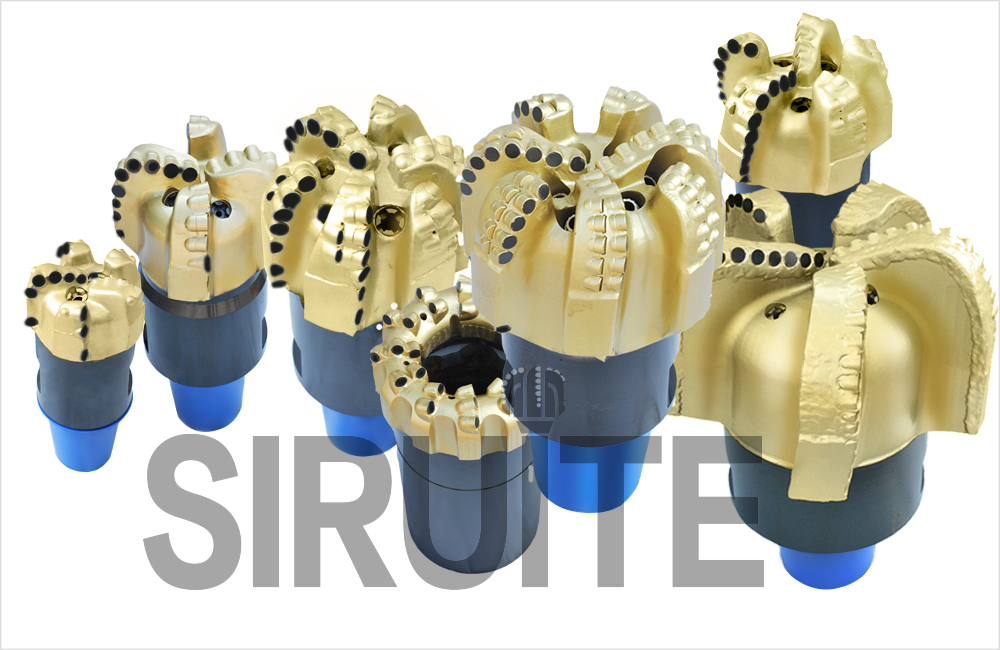
“Matrix” is a very hard, rather brittle composite material comprising tungsten carbide grains metallurgically bonded with a softer, tougher, metallic binder. Matrix is desirable as a bit material, because its hardness is resistant to abrasion and erosion. It is capable of withstanding relatively high compressive loads, but, compared with steel, has low resistance to impact loading.
Matrix is relatively heterogeneous, because it is a composite material. Because the size and placement of the particles of tungsten carbide it contains vary (by both design and circumstances), its physical properties are slightly less predictable than steel.
Matrix body bits are manufactured by mold process. The tungsten carbide and binder materials are arranged into the mold. The mold get placed in to the furnace for certain period of the time and materials are cooked to certain temperature. The mold later cooled down and broken to remove the unfinished matrix bit.
Steel-body PDC Bit
Steel is metallurgically opposite of matrix. It is capable of withstanding high impact loads, but is relatively soft and, without protective features, would quickly fail by abrasion and erosion. Quality steels are essentially homogeneous with structural limits that rarely surprise their users.
Steel body bits are manufactured by machining the steel bars per design.
Design of matrix and steel-body bits
Design characteristics and manufacturing processes for the two bit types are, in respect to body construction, different, because of the nature of the materials from which they are made. The lower impact toughness of matrix limits some matrix-bit features, such as blade height. Conversely, steel is ductile, tough, and capable of withstanding greater impact loads. This makes it possible for steel-body PDC bits to be relatively larger than matrix bits and to incorporate greater height into features such as blades.
Advantage of matrix-body PDC bits
Matrix-body PDC bits are commonly preferred over steel-body bits for environments in which body erosion is likely to cause a bit to fail. For diamond-impregnated bits, only matrix-body construction can be used.
Advantage of steel-body PDC bits
The strength and ductility of steel give steel-bit bodies high resistance to impact loading. Steel bodies are considerably stronger than matrix bodies. Because of steel material capabilities, complex bit profiles and hydraulic designs are possible and relatively easy to construct on a multi-axis, computer-numerically-controlled milling machine. A beneficial feature of steel bits is that they can easily be rebuilt a number of times because worn or damaged cutters can be replaced rather easily. This is a particular advantage for operators in low-cost drilling environments.
Cosiderning the fact that cost is a major aspect in drilling and that tungsten carbide is more expensive than high alloy steel, steel body PDC drill bits have a larger market share.
Development of PDC bits
Fortunately, both steels and matrix are rapidly evolving, and their limitations are diminishing. As hard-facing materials improve, steel bits are becoming extremely well protected with materials that are highly resistant to abrasion and erosion. At the same time, the structural and wear-resisting properties of matrix materials are also rapidly improving, and the range of economic applications suitable for both types is growing.
Today’s matrix has little resemblance to that of even a few years ago. Tensile strengths and impact resistance have increased by at least 33%, and cutter braze strength has increased by ≈80%. At the same time, geometries and the technology of supporting structures have improved, resulting in strong, productive matrix products.